Clientcases
4PLUS
Renewal of the entire IT landscape
4PLUS values quality and reliable delivery of building materials to Dutch family businesses. 4PLUS is a fast-growing company with 55 affiliated partners and an assortment of over 700,000 items. In order to meet the demands of this constantly changing market in the future, 4PLUS decided to renew the entire IT landscape simultaneously. A modern Warehouse Management System to control the wide variety of logistical processes within the warehouse could not be left behind. "Vanboxtel also contributed to a seamless integration with our new ERP system," according to Richard Voorter, Manager of IT at 4PLUS.
"For 4PLUS, the biggest challenge was renewing the entire IT landscape over one weekend, with the WMS being an important part. Vanboxtel proved to be a reliable partner in this process, adhering to the schedule as planned."
More about this case
A good match
"Besides looking for a WMS, we really focused on the people and the (family) organization behind the product itself, where a good match is essential for a strategic and long-term cooperation." 4PLUS gave Vanboxtel the confidence to find a suitable solution that fully fits the organization. "The fact that our current handterminals were taken into management by Vanboxtel and could be reused was a nice windfall," said Kees Machielse, director of 4PLUS. "Vanboxtel has the needed expertise to take on any logistical challenge. They critically analyze the problem and provide an appropriate solution."
"The direct lines of communication and clear interactions with Vanboxtel’s project manager kept the project team on their toes and ensured that we stayed on schedule throughout the project."
A wide variety of goods arrive daily from a wide range of suppliers at the logistics center in Born, where there is a warehouse with a storage capacity of over 20,000 pallet spaces. Depending on the specific product characteristics, these goods, supported by Vanboxtel’s WMS, eventually find the most optimal place in the warehouse.
"Our affiliated family businesses can place orders throughout the day. Because Vanboxtel allows us to combine these individual orders into one pick order per zone, we are able to pick our orders efficiently."
Management and planning
As part of the WMS implementation, an entirely new location structure was set up as advised by Vanboxtel. This makes the stock allocation in the warehouse more logical and easier to locate for the warehouse employees. The new structure also makes it possible for 4PLUS to easily make its own adjustments to the locations and zoning.
Every day, several trucks depart for various businesses throughout the Netherlands. Vanboxtel’s WMS supports 4PLUS in creating the most efficient trip planning. This can be quite a puzzle due to the diversity of products, dimensions, and weights of building materials.
Implementation and result
To involve warehouse employees in this process as well, Vanboxtel regularly visited 4PLUS's warehouse during the implementation phase to provide training and assist with testing the entire system. Since early December 2023, Vanboxtel’s WMS has been live and is indispensable to 4PLUS's daily operations. "The changes in our work processes were intensive, but the improvements in our warehouse are visible and have paid off!" With access to real-time data from the complete WMS, 4PLUS gains deeper insights into logistics processes and key metrics. Inventory has also become a lot easier and more reliable. As a result, we already notice that we have gained more control over our stock.
Within one week, 4PLUS was working completely independently with Vanboxtel’s WMS. Whenever there are questions and/or remarks, 4PLUS can always rely on the support of Vanboxtel, which is available 24/7.
Relevant solutions with this client case
Vanboxtel-WMS
Support / service
Warehouse assets
Want to know more about the used services?
Want to know more about this case and the services that are offered? Feel free to contact us., we will answer your questions as soon as possible.
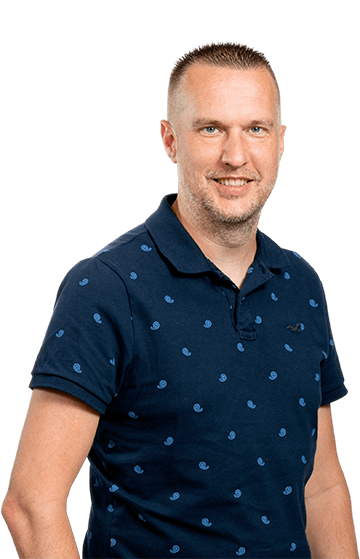